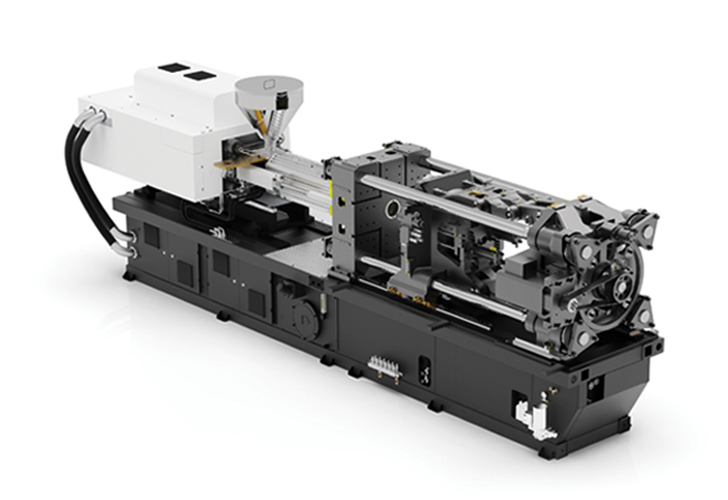
Enjeksiyon Prosesinde Yaşanan Problemler ve Çözümleri
Enjeksiyon makinesinin, kalıbın ve malzemenin performansı zaman, basınç ve sıcaklık değişkenlerine bağlıdır.
21-09-2022
Plastik makinelerinde, plastiğin eritildiği ve şekil verilebilir hale getirildiği kısım kovan ve vidadır.
Plastiğin Erime Karakteri, Erime Davranışı ve Kovan-Vida Sistemlerinin Eriyik Kalitesine Etkisi
Polimerler ısı ve shear stres etkisi altında, kristal yapılarını ve bağ yapılarını değiştirerek fiziksel olarak dönüşüm gösterirler. Fiziksel hal değişimini ve bu değişim karakterini etkileyen en önemli şey elbette kimyasal ve molekül hareketleridir. Aynı kimyasal bileşime sahip polimerlerde dahi yarı kristalin ya da amorf yapıda olunması bu karakteri mutlaka değiştirir.
Polimerik malzemeleri karakterize etmek için kullanılan iki ana geçiş sıcaklığı vardır:
Erime sıcaklığı (Te) ve camsı geçiş sıcaklığı (Tg)
Kristalleşebilen polimerlerin % 100 kristal yapıda olmasının ancak teorik olarak mümkün olabileceğini belirtmiştik. Yarı kristal bir polimerin kristalize olmuş zincirlerinin erimeye başladığı sıcaklık polimerin erime sıcaklığı olarak kabul edilir. Amorf yapıda bulunan kısımların ise soğuma sırasında yumuşak kauçuğumsu yapıdan, sert, kırılgan ve katı (rijit) camsı yapıya geçtiği sıcaklığa ise camsı geçiş sıcaklığı denir.
Polimerin ısı karşısındaki davranışları, yapılarında amorf ya da kristal bölgelerin varlığına yakından bağlıdır. Amorf polimerler ısıtıldıklarında önce camsı geçiş sıcaklığından geçerek camsı yapılardan kurtulur ve elastiki hale kavuşurlar. Daha yüksek sıcaklıklara ısıtıldıklarında ise zamksı davranışa ve sıvılaşmaya uğrarlar. Bu hareketlerinin artışından kaynaklanan bir akışkanlık, ya da sıvılaşmadır.
Yarı-kristal polimerler ise önce camsı geçiş sıcaklığından geçerek camsı yapıdan elastiki yapıya ulaşırlar. Daha yüksek sıcaklıklarda ise amorf yapılarının içinde oluşan kristal yapıları erimeye başlar ve eriyik halde bir polimer oluştururlar.
Erime esnasında polimere uygulanacak yüksek ısı, yüksek shear stres ya da basınçtan dolayı ya da bunun tam tersi durumdan ötürü polimer eriyiğinin kalitesi etkilenecektir. Polimerin erime prosesinin gerçekleştiği kovan-vida grubunda doğru dizayn ve doğru malzeme kullanımı son derece önemlidir.
Plastik ürün üretiminde plastiğin erime mekanizması ve karakterine uygun olmayan bir yöntem ile kaliteli bir eriyik yapısı elde edilemez. Plastiğin eriyik karakterine uygun bir kovan-vida grubu seçilmelidir. Her plastik hammadde ve her prosese özel kovan ve vida dizaynları olduğu gibi birçok polimeri işleyebilecek üniversal dizaynlarda mevcuttur.
Enjeksiyon Uygulamalarında Kovan-Vida Sistemlerinin Önemi
Plastik makinelerinde, plastiğin eritildiği ve şekil verilebilir hale getirildiği kısım kovan ve vidadır. Dolayısı ile plastiğin eriyik kalitesine, homojenliğine ve bu eriyikten elde edilecek ürünün kalitesine doğrudan en fazla etki eden bileşen her zaman kovan ve vidadır. Plastik ürünün kalitesinde eriyik kaynaklı yaşanan problemlerin %80 inde problemin kaynağı, kovan ve vida gruplarının yanlış dizayn ya da aşınma sonucu görevi yerine getirmemesindendir. Bu durum kova ve vida sisteminin plastiği ergitme, taşıma ve sıkıştırma işlerini üstlenmiş olması dolayısı ile en fazla yorulmaya ve aşınmaya maruz kalmasının bir sonucudur.
Polimerlerin erime proseslerinin gerçekleştiği kovan ve vida grubunda doğru dizayn ve doğru malzeme seçimi son derece önemlidir. Farklı prosesler, farklı plastik malzemeler ve farklı kapasite ihtiyaçlarına bağlı olarak, eriyik kalite unsurunu en üst seviyede tutabilecek şekilde tasarlanan kovan ve vida sistemlerinin, bir çok polimeri işleyebilecek şekilde üniversal dizaynları da bulunmaktadır.
İlgili proses ve polimer karakterine uygun olmayan kovan ve vida kullanımından dolayı şu sorunların yaşanması muhtemeldir.
* Yeterli erime sağlanamaz.
* Uygun eriyik kalitesine ulaşılamaz.
* Eriyikte homojenlik sağlanamaz.
* Üründe yeterli mekanik dayanım elde edilemez.
* Düşük kapasite ve düşük enerji verimliliği ile üretim yapılır.
* Kovan ve vida sistemlerinde hızlı aşınma ve yıpranmaya sebep olur.
* Kalıp ve ona bağlı tüm bileşenlerde bir çok hasara sebep olabilir.
Günümüzde gelişen teknolojinin de getirdiği avantajlar ile plastik işleme proseslerinin ihtiyaçlarını karşılayacak bir çok AR-GE çalışmalara yapılmaktadır. Konusunda uzmanlaşmış ve üstün tasarım kabiliyetine sahip kurumlar ve kişiler tarafından yapılan bu AR-GE çalışmaları sonucunda kovan-vida sistemlerinde yüksek ergitme kabiliyeti, yüksek kapasite ve performans, üstün aşınma direnci ve düşük üretim maliyeti avantajı sağlanmış, basit yapılı ürünlerden en kompleks ve karmaşık karakterdeki ürünlere kadar olan tüm ihtiyaçlara cevap verilebilir duruma gelinmiştir.
Enjeksiyon Uygulamalarında Kovan-Vida sistemlerinin Şekil Tanımı ve Temel Boyutlandırma
Enjeksiyon uygulamalarında kullanılan kovan-vida sistemlerinde, görüntü itibari ile hangi bölümlerden oluştuğu ve temel boyutlandırmada kullanılan terim ve tekniklerin bilinmesi, hem üretici hem de kullanıcıların ortak bir dilde buluşmasını sağlamakta ve faydalı olmaktadır.
Dünyada Plastik teknolojileri adı altında yapılar tüm çalışmaların, ortak dilde konuşulması ve belirli standartlarda uygulanabilmesi için EUROMAP normları oluşturulmuştur. Bu standartlar dahilinde enjeksiyon kovan-vida sistemleri de plastik işleme yeteneğini sınıflandırma ve boyutlandırma açısından çap (D) ve boy (L) ölçülerinin belirli bir oranına bağlı olarak mal edilmektedir.
L/D olarak tanımlanan bu oran, vide efektif boyunun çapına oranı olup vidanın ilgili plastiği eritme ve işleme boyunu göstermektedir.
Basit yapılı bir enjeksiyon kovanı ve vidası ele alındığında, vidanın sürücü boyu haricinde kalan diğer kısmı hatve boyu L (genel) olarak adlandırılır. Ancak L/D oranındaki L boyu, kovanın penceresinden itibaren başlayan yani plastik hammaddenin erimeye başladığı L (efektif) boyudur. Her proses için standart oluşturulmuş olan bu oranla gelişen plastik teknolojisi ile farklılıklar da gösterilmektedir.
Enjeksiyon Uygulamalarında Kovan-Vida Sistemleri ve Çalışma Prensibi
Enjeksiyonda kullanılan kovanlar, proses sırasında oluşan yüksek basınca karşı dayanıklılık ve kararlılık göstermelidir.
Enjeksiyon sırasında, yüksek enjeksiyon basıncına bağlı olara kovan içi çapı esneyerek genişleme eğilimi gösterir.
Kovan dizaynı, malzeme seçimi ve sertleştirme metodu kovan iç çapı ile roket grubu bileziği arasındaki dar boşluğu koruyacak şekilde seçilmeli, hassasiyet sürekliliğini sağlama açısından aşınma direnci yüksek malzemeler kullanılmalıdır.
İdeal enjeksiyon prosesi için, kovan iç çapı ile vida dış çapı, kovan iç çapı ile roket grubu bilezik dış kapı arasında hassasiyetle seçilmiş dar boşluklar bırakılmalıdır.
ENJEKSİYON VİDA TASARIMI
Basit bir enjeksiyon vidası şu bölümlerden oluşur:
Besleme bölgesi (Katı taşıma, Feeding Zone)
Besleme bölgesi vidanın huniden malzeme aldığı kısmıdır. Bu bölgenin görevi huniden aldığı granül veya toz hammaddeyi vida kanalına aktarmaktır. Genellikle bölgede hatve derinliği sabittir. Bu hatveler sayesinde plastik malzeme belirli bir basınç artışı sağlanarak besleme hunisinden alınarak ileriye doğru itilir. Bu bölgede hammaddenin ilerlemesi, vida üzerinde kaymasına ve kovana sürtünerek tutunmasına bağlıdır.
Eritme Bölgesi (Melting or transition zone)
Bu bölgenin görevi, beslenen plastiği eritmektir. Bu bölge boyunca granüller halindeki hammadde eriyerek bir eriyik havuzu halini alır. Klasik vidalarda hammadde, bölge boyunca kovana doğru bastırılarak eritme sağlanır. Böylece plastik sıkıştırılıp basıncı arttırılarak dozajlama bölgesine gönderilir. Besleme bölgesindeki hacimsel büyüklüğün dozajlama bölgesindeki hacimsel büyüklüğe oranı vidalarda ‘’kompresyon oranı’’ olarak adlandırılır.
Dozajlama Bölgesi (Pompalama-Metering or pumping zone)
Vidanın en önemli bölgesidir. Eritilen plastiğin kalıptan çıkması için gereken basıncı oluşturur.
Vida içerisindeki basınç dağılımı klasik 3 bölgeli vidalarda hammadde besleme işleminden, kalıp çıkışına kadar sürekli artan bir faktör olmaktadır. En iyi enjeksiyon şartları, maksimum seviyede homojenize edilmiş ve eritilmiş hammaddenin, istenen basınç değeri ile kalıba gönderilmesi ile elde edilir.
Vidada basınç kalıba yaklaştıkça artar. Kalıba ulaşan malzeme enjeksiyonda gerekli basınç değerine çıkarken vidanın sıkıştırma kuvvetinden çok, hidrolik sisteminin itiş gücü ile ulaşır.
ENJEKSİYON VİDASI TİPLERİ VE ÇALIŞMA PRENSİPLERİ
Vida hareketi ile hem ilerleyen, hem de basıncı ve dolayısı ile sıcaklığı artan hammaddenin katı fazdan eriyik fazına geçişinde dizayn olduşça etkilidir.Farklı dizayna sahip vidalarda , vida geometrisi boyunca katı ve eriyik fazlarının dağılımı farklı olmaktadır. Genel olarak enjeksiyon vidaları hatve yapısı geometrileri bakımından iki gruba ayrılır.
* Düz Hatveli Vidalar
* Barrier Hatveli Vidalar
Vidanın dışarıdan aldığı tahrik ile hareketi sayesinde, hammadde hatve kanallarında taşınır, ısıtıcıların da etkisi ile eritilir, karıştırılır ve kalıba doğru iletilir.
Barrier Vida Teknolojisi
Gelişen polimer teknolojisine paralel olarak zor eriyen, zor şekillenen fakat mekanik ve ısıl özellikleri yüksek polimerlerin kullanımının artması ile polimer işleme teknolojisi de gelişmiştir. Düz vida tasarımı ile işlenemeyen polimerlerin işlenebilmesi için yeni dizaynlar denenmiştir.
Bariyerli vidalar ortak mantık temelinde fakat farklı geometrilerde üretilmektedir. Geometrik bakımdan bariyerli vidalar ikiye ayrılır:
* Barr Vidalar
* Maillefer Vidalar
Barr Vidalar
Barr vida, düz vidadan farklı olarak ana hatvenin yanında bir yardımcı hatveye sahiptir. Bu yardımcı hatve sabit genişlikte fakat gittikçe derinleşerek ilerler. Eriyen plastik derinleşen kanala transfer olurken katı plastiğin bulunduğu kanalın derinliği gittikçe azalarak plastiğe bir kompresyon uygular. Böylece eriyen plastik bozulmadan taşınırken erimeyen plastiğe sığlaşan kanalın uyguladığı kompresyonla hızlı ve kaliteli bir eritme sağlanır.
Barr vidada eriyik bölgesi sığ olarak başlar. Vida boyunca kalıba yaklaştıkça katı faz bölgesi adeta bir pistonun sıkıştırdığı gibi sıkışıp daralırken, eriyik bölgesi derinleşir. Katı faz tamamen eriyik haline geldiğinde barrier hatve, ana hatve üzerine kapanır.
Maillefer Vidalar
Maillefer vida tasarımında yardımcı hatve ile ana hatve arasındaki derinlik değişmez. Fakat barr vidasının aksine yardımcı hatve genişliği sabit kalmaz, sıfırdan başlayıp gittikçe artarak sonunda ana hatve üzerine kapanır. Yani plastiğin taşınma yönünde yardımcı hatve ile ana hatve arasında olan katı faz, vida ilerledikçe azalır ve eriyik faz büyür. Yardımcı hatve ana hatvenin üzerine kapandığında artık katı plastik kalmamıştır.
Barrier Vidaların Avantajları;
Hızlı eritme,
Sabit, yüksek debi,
Minimal tazyik ve eriyik ısısı değişimi,
Daha iyi eriyik kalitesi,
Daha iyi dispersif karıştırma,
Klasik vidalara oranla çok daha yüksek turlarda kaliteli eriyik sağlandığından daha yüksek kapasitelere ulaşma imkanı,
Rejenere edilmiş veya hurda malzemelerin çok daha iyi işlenmesi.
Enjeksiyon Vidalarında Prosese Etki Eden İlave Karıştırıcılar
Ürün kalitesini arttırmak için enjeksiyon vidalarına standart bölgeler dışında başka bölgeler de ilave edilir. Örneğin vidanın çıkış bölümüne karıştırıcı mikserler ilave edilerek plastik eriyiğinin daha iyi homojenize edilmesi sağlanabilir.
Vidalarda daha iyi bir karışım için, masterbatch yada diğer katkı maddelerinin eriyik içerisinde en iyi dağılımı için karıştırıcı bölümler eklenir.Karıştırıcılar fonksiyonları açısından ikiye ayrılır;
Dispersif Karıştırıcılar
* Karışımdaki farklı boyutların ve fazların aynı boyutta olmasını sağlayan karıştırmadır.
* Eriyik ve içerisindeki katkı maddelerinin sığ bir kesitten zorlanarak enine ve boyuna kesme gerilimi uygulaması ile elde edilir.
* Malzemeyi eritmeye katkı sağlar.
Distribütif Karıştırıcılar
Karışım içerisindeki katkıların ve ısının her noktada eşit oranda karışım sağlayarak kusursuz bir homojen yapı oluşturmasını sağlar. Bu karışım içinde mikser ile çırpma işlemi gibi tanımlanabilir.
Enjeksiyon Makinesinde Kovan-Vida Sistemlerinin Kuruluma ve Doğru Montaj Teknikleri
Sağlıklı bir proses gerçekleştirme, öncelikle prosesin yapılacağı alanın seçimi ile başlamalıdır. Seçilecek olan alan, proseste kullanılacak olan tüm ekipmanları bünyesinde barındıracak şekilde olmalıdır. Konumlandırmadaki en önemli nokta, enjeksiyon makinesinin konulacağı alanın kapı ve pencere gibi hava koridoru oluşturulabilecek yerlerde olmaması gerektiğidir. Böyle bir durum prosesteki ve özellikle kovan ve kalıptaki sıcaklık dengesini bozmakta, nihai üründe dalgalanmalara neden olmakta ve birbirleri ile hassas dengede çalışan tüm ekipmanların senkronize olmalarını engellemektedir.
* Enjeksiyon makinesi başta olmak üzere tüm ekipmanların oldukça düzgün bir zemine, ayarlanabilir ayaklar ile konumlandırılarak aynı eksende olacak şekilde ayarlanarak teraziye alınması ve montaj yapılması gerekmektedir.
* Montaj anında enjeksiyon makinesi ve diğer ekipmanların konumlandırılmasında vibrasyon önleyici sistemlerin kullanılması sonradan oluşacak titreşimlerin getireceği olumsuzlukları engelleyecektir.
* Enjeksiyon makinesi ve ekipmanlarının tüm mekanik bağlantı noktaları kontrolden geçirilmelidir.
* Enjeksiyon makinesi ve ekipmanlarının elektrik, elektronik, pnömatik veya hidrolik aksamları kontrol edilmeli, taşıyıcı kablo, hortum, boru gibi tesisatlar proses çalışması sırasında veya bakım anında çalışmaları engellemeyecek şekilde ideal pozisyona getirilmelidir.
* Enjeksiyon makinesine montajı yapılacak olan kovan-vida sisteminin ilgili prosese uygunluğu kontrol edilmelidir.
Kovan Vida Montajı Sırasında Dikkat Edilmesi Gereken Hususlar
* Enjeksiyon kovanlarının, plaka oturma yüzeyleri, meme gövdesi ve memenin birleşme noktalarında, flanş oturma ve alın basma yüzeylerinde herhangi bir deformasyon olup olmadığı kontrol edilmeli, pürüzsüz yüzey sağlanmalı, pas veya korozyona karşı yüzeylere ısıya dayanıklı ince yanmaz yağ sürülmelidir.
* Kovan zemine yatay olacak şekilde bir kaldırma vasıtası ile redüktör ve ayarlı kovan yataklama parçasına eksen düzgün olacak şekilde konumlandırılmalıdır. Kovan ve vida doğrusallığı aynı eksende enjeksiyon kalıbı ile eşmerkezde olmalıdır. Bu kovanın sağlıklı çalışması için çok önemlidir.
* Kovanın tüm birleşme yerlerindeki yuvaların tam oturduğu kontrol edilmeli, terazisi ayarlanarak bağlantı civataları ve tespit somunları belirli bir düzende sıkılmalıdır.
* Kovan montaj ve meme bağlantı civataları takılmadan önce civataların dişlerine sıcak montaj pastası sürülmesi, civataların her sökülüp takılmasında hem zorlanılmaması hemde dişlerin zarar görmemesi için idealdir.
* Tüm civatalar sıkıldıktan sonra kovanın terazisi bir kez daha kontrol edilmelidir.
* Kovan ve vida montajının eksiksiz yapıldığından emin olduktan sonra besleme hunisi sistemi, ısıtıcı rezistans ve soğutma üniteleri kovana monte edilmelidir.
* Hangi proses olursa olsun enjeksiyon uygulamasının sağlıklı yapılabilmesi için özellikle kovan-vida sistemlerinin uzun ömürlü olması için plastik hammadde içine karışmış olabilecek veya başka kaynaklardan gelebilecek aşındırıcı ve zararlı cisimlerin kovan içerisinden kaçmasını engelleyen besleme filtreleri kullanması gerekmektedir.
* Kovan ve vida bağlantısının akabinde herhangi bir sorun olmadığından emin olunduktan sonra elektrik aksamları ve buna bağlı sistemler kontrol edilerek devreye alınır.
* Proseslerde kullanılan enjeksiyon vidaları genelde sağ hatveli olup, tam tersi sol istikamette dönerek çalışmaktadırlar, buna karşılık bazı proseslerde sol hatveli vidaların kullanılması vidanın sağ istikamette döndürülmesini gerekmektedir.
* Bu önemli ayrıntı için proses başlamadan önce hidromotorun dönüş yönünün ilgili vida için uygun olup olmadığı kontrol edilmelidir.
ENJEKSİYON PROSESİNE HAZIRLIK VE SAĞLIKLI ÇALIŞMA ÖNERİLERİ
* Bir enjeksiyon makinesi ve bağlı tüm ekipmanın kullanımı ve kontrolü, bu konuda daha önceden eğitim almış dahi olsa tekrar eğitim verilerek uzmanlaştırılmış personel tarafından yapılmalıdır.
* Enjeksiyon prosesi sırasında çıkan sorunların çoğu genellikle gece vardiyalarında oluştuğundan, bu vardiyada çalışacak olan personel gündüz istirahatine dikkat etmeli, yorgun ve uykusuz gece vardiyasına başlamamalıdır.
* Varsa kovana otomatik hammadde taşıyan kanalların ve besleme hunisinin akış yolunda herhangi bir engelleyici durum olup olmadığının kontrolü yapılmalıdır.
* Sistemin çalışma aşamasında, vida döndürülmeye başlanmadan önce kovan ve çıkıştaki kalıp üzerindeki ısıtıcılar, hammaddenin eriyik özelliğine göre bölge bölge ısıları ayarlanarak kademeli olarak set edilmeli kovan ve kalıp ısıtılmalıdır.
* Isıtma işlemi sonrası genleşmeler sebebiyle kovan birleşme yerlerinden civatalarının sıkılığı tekrar kontrol edilip gerekirse tekrar sıkılmalı, uygun sıcaklığa ulaştığında vida oldukça yavaş bir hız ile çevrilerek herhangi bir mekanik sorun olup olmadığı kontrol edilmelidir.
* Isılar kararlı bir durumda olduğu ve mekanik bir sorun olmadığı görüldükten sonra hammadde beslemesi yapılır.