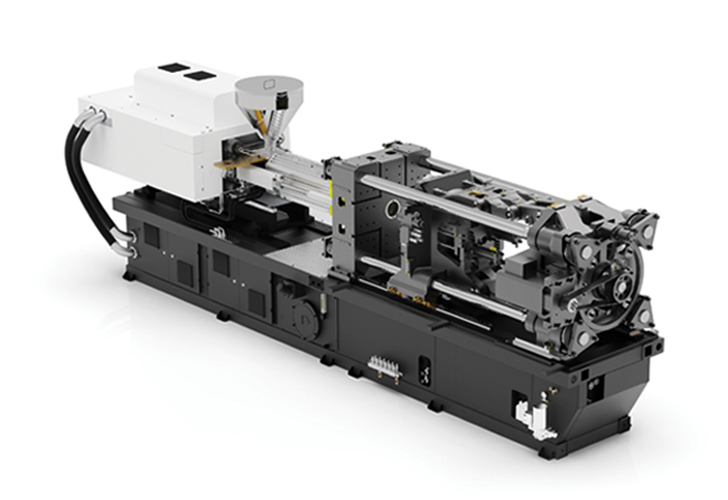
Enjeksiyon Prosesinde Yaşanan Problemler ve Çözümleri
Enjeksiyon makinesinin, kalıbın ve malzemenin performansı zaman, basınç ve sıcaklık değişkenlerine bağlıdır.
21-09-2022
Enjeksiyon kalıplama, plastik parçaların üretiminde kullanılan en yaygın yöntemdir.
ENJEKSİYON KALIPLAMA
Plastik parçaların üretiminde kullanılan en yaygın yöntemdir. Süreç ısıtılan eriyik plastiğin üretilecek parçanın şeklindeki kalıba enjekte edilmesini içermektedir. Soğuma ve katılaşma sonrasında parça çıkartılır ve süreç devam eder.
Enjeksiyon kalıplama süreci ile diş, yay, menteşe gibi sınırsız çeşitlilikle detay içeren sınırsız çeşitlikle parçaların tek bir kalıplama operasyonuyla üretilmesi mümkündür.
Enjeksiyon kalıplama yöntemi ile kritik boyutlar ve duvar kalınlığı yönünden tutarlı, yüksek kaliteli parçalar üretilmekte ve bu yöntem genellikle seri üretim ve prototip üretiminde kullanılmaktadır.
Enjeksiyon makinesinde, enjeksiyon ve mengene ünitesi olmak üzere 2 ana bölüm bulunmaktadır.
Enjeksiyon ünitesi besleme haznesi vidayı (veya pistonu) çevreleyen ısıtılmış enjeksiyon kovanı, hidrolik motor ve enjeksiyon silindiri içermektedir. Sistem termoplastiği uygun viskoziteye ısıtarak ve kalıba enjekte ederek çalışmaktadır. Beslenme haznesine gelen reçine ısıtıcılarının bulunduğu enjeksiyon kovanına girer ve vidanın dönüşüyle ileriye taşınır. Isıtılmış kovanın içerisinde eriyik paletleri karıştıran ve kovanın ucuna yönlendiren motorlu vida bulunmaktadır. Eriyik halde olan plastik, vida (bazı makinalarda Ram) tarafından hızı ve basıncı kontrol edilerek yolluklardan geçer ve kalıbın içine yerleştirilir.
Mengene ünitesi kalıp plakalarına hidrolik basınç uygular ve makas sistemi mekanik olarak kilitleme kuvvetini güçlendirir. Bileşenlerin şekillendirildiği kalıbın dişi ve erkeğini bir arada tutması nedeniyle pres adı da verilmektedir. Sıkıştırma sisteminin fonksiyonu plastiğin dışarı taşmasını ve ‘’çapak’’ yapmasını engellemek için tüm enjeksiyon süreci sırasında kalıbın kapalı kalmasını sağlamaktır.
Sıcak materyal kalıptaki tüm boşlukların doldurulması için yüksek basınçla kalıp içerisine enjekte edilir. Plastik soğumaya ve kalıp içerisinde katılaşmaya bırakılır. Kalıp içerisinde soğuk su gezdirilerek içeriden soğutulur. Soğutma sonrasında mengene açılır, bu ünite kalıbın iki yarısını birbirinden ayırır. İtici çubuğu ve plakası bitmiş parçayı kalıp dışına iter. Çıkan yolluklar ve kusturulan mal tekrar kullanılmak üzere geri dönüştürülebilir.
Termosetlerin enjeksiyon kalıplaması termoplastiklerin enjeksiyon kalıplamasına benzerdir, fakat materyal, çapraz bağlanma meydana gelebilmesi için ısıtılmış kalıp içerisinde soğutularak bekletilir. Sonrasında kalıp açılır ve sıcak fakat sert parça çıkartılır.
Enjeksiyon makineleri temel olarak kendilerini çalıştıran sistem türüne göre sınıflandırılır:
* Hidrolik
* Tam elektrikli veya hibrid
Hidrolik enjeksiyon makinelerinde, sıkıştırma mekanizması olarak makas sistemi kullanılmaktadır. Bu makine türü kalıplama şirketlerinin birçoğu tarafından kullanılmaktadır.
Elektrikli enjeksiyon makineleri her bir eksene bağlı servo motorlar tarafından çalıştırılır. Tüm kalıplama döngüsü boyunca silindire hidrolik pompalayan hidrolik makinelerinden farklı olarak tam elektrikli makine yalnız makine hareket halinde iken enerji harcar. Kilitleme için makaslı mengene sistemini kullanmaktadır. Daha hızlı, daha sessizdir, daha yüksek hassasiyete sahiptir ancak daha pahalıdır.
ENJEKSİYON KALIPLAMA MAKİNASININ DOĞRU SEÇİMİNDE DİKKATE ALINACAK HUSUSLAR
Enjeksiyon kalıplama makinası; tek çevrimde enjekte edilebilecek gram cinsinden malzeme miktarına (10 gramdan birkaç kiloya kadar) ve makinenin uygulayabileceği sıkıştırma kuvvetini temsil eden tonaja (5 tondan daha düşük seviyelerden 6000 tona kadar) göre tanımlanmaktadır.
Örneğin;90 gram ve 60 tonluk makine gibi.
* Makinenin gramajı, parçalar ve yolluğun (çoklu boşluklar) toplam ağırlığından daha fazla olmalıdır.
* Enjeksiyon basıncı yeterli olmalıdır.
* Sıkıştırma tonajı enjeksiyon basıncından yüksek olmalıdır.
* Vida tasarımı işlenecek materyale uygun olmalıdır.
* Günışığı açıklığı kalıp boyutu, parça yüksekliği ve parçanın çıkartılması için gerekli boşluğun toplamından daha fazla olmalıdır.
* Kolon milleri arasındaki mesafe kalıp boyutundan fazla olmalıdır.
ENJEKSİYON KALIPLAMA SÜRECİ
AVANTAJLARI
* Yüksek üretim çıktı oranlarıyla düşük maliyetler
* Yüksek hassasiyet ve doğruluk
* Küçük detaylı parçalarda yakın toleranslar mümkündür
DEZAVANTAJLARI
* Yüksek yatırım maliyetleri
* İşleme pahalıdır ve daha uzun zaman gerektirir
ENJEKSİYON BASKI TÜRLERİ
İNSERT KALIPLAMA
İnsert kalıplama bir obje veya insertin çevrimler arasında kalıp boşluğuna yerleştirilmesi ve plastiğin insert etrafından enjekte edilmesi, böylelikle insertin son kalıplı ürünün bir parçası haline gelmesi işlemidir. İnsert olarak kullanılan malzemeler arasında çeşitli metalik insertler, kumaş, segman ve film bulunmaktadır. İnsert kalıplama ürünleri için insertin kalıp boşluğuna yerleştirilmesini kolaylaştırmak amacıyla kalıbın dikey olarak açıldığı ve kapandığı Dik Enjeksiyon Makinesi kullanılmaktadır. Örneğin; bıçak tutacakları, tornavidalar, uygulama kabini.
YAPISAL KÖPÜKLÜ KALIPLAMA
Köpüklü kalıplama düşük basınçlı enjeksiyon kalıplama sürecidir. Köpük erime süreci sırasında basınç altında soy gaz ve reçinenin karıştırılmasıyla veya reçineye eklenen kimyasal şişirme ajanının bozulmasıyla ortaya çıkan gazlarla oluşmaktadır. Karışım kalıba enjekte edilirken, malzeme basınçsızlaştırılır ve gazın genleşerek hücresel bir çekirdek oluşturmasına izin verilir. Köpük parçalar genellikle köpükler sebebiyle düşük ve belirli yoğunluğa sahip kalın duvar bölümlerinden oluşurlar. Parçalar mükemmel kuvvet-ağırlık oranına, gelişmiş termal ve akustik yalıtım özelliklerine sahiptir fakat düşük gerilme kuvvetleri mevcuttur. Kullanılan kalıplar daha ucuz ve daha hafiftir(takım çeliği yerine alüminyum) ve daha büyük parçalar üretmek için kullanılabilir. Düşük kurulum maliyeti Yapısal köpüklü kalıplamayı düşük hacimli uygulamalar için enjeksiyonlu kalıplama karşısında cazip kılmaktadır. Sıklıkla kullanılan polimerler şunlardır; HDPE, ABS, PP ve LDPE. Uygulamalar polistiren içecek bardakları, ambalaj materyalleri, yalıtım panelleri ve fast food kartonları gibi sert ürünlerdir.
GAZ DESTEKLİ ENJEKSİYON KALIPLAMA
Gaz destekli kalıplama eriyik polimerin kısmen veya tamamen kalıp boşluğuna enjekte edilmesinden sonra basınç altında kalıba azot gazı uygulanmasını içermektedir. Bu uygulama ile çöküntü oluşmayan içi boşluklu sert parçaların üretimi gerçekleştirilir. Kalıplanan malzemenin kalın bölümlerinin içerisinde boşluk açılarak parça ağırlığında azalma sağlanır, reçine malzemesi tasarrufu, daha kısa soğutma döngüleri, azalan sıkıştırma kuvveti tonajı ve parça konsolidasyonu sağlanır. Bu şekilde oluşan gaz kanalları aynı zamanda reçinenin akışını etkili biçimde desteklemekte ve kalıplama basıncının büyük oranda azalmasını sağlamaktadır, karşılığında iç gerilimler azalmakta, tek tip kalın çekmesi yaşanmakta ve çöküntü çarpıklık azalmaktadır
KOENJEKSİYON (SANDVİÇ) KALIPLAMA
Koenjeksiyon sandviç kalıplamada iki farklı fakat uyumlu eriyik polimer sırayla soğuk kalıba enjekte edilir, kabuk/çekirdek yapısı oluşturulur. Öncelikle boşluk kısmen dış kabuğu oluşturan materyal ile doldurulur. Bunun sonrasında çekirdek bileşen birinci materyalin plastik çekirdeği içine enjekte edilir. Son olarak birinci bileşen ile birlikte yolluk alanında conta oluşturulabilir, böylelikle çekirdek materyalin yüzeye penetre etmesi engellenir ve yolluk sistemi aynı zamanda gelecek baskı için temizlenerek sandviç kısmını oluşturur.
REAKSİYON ENJEKSİYON KALIPLAMA (RIM)
Çekirdekte geri dönüşümlü materyal kullanma olanağı sürecin temel avantajları arasındadır. Büyük miktarlarda geri dönüşümlü plastik özelliklerde herhangi bir kayıp olmadan ürünler de yeniden kullanılabilir böylece orijinal maldan üretilebilen kabuk özellikler ve görünüme hakim hale gelir.
Reaksiyon Enjeksiyon kalıplama (RIM) iki sıvı bileşenin kalıp içerisine enjekte edildiği ve sıvılar arasındaki kimyasal reaksiyonun katı plastik bir parçanın oluşmasıyla sonuçlandığı bir süreçtir.
Tipik olarak iki sıvının izosiyanat ve polidrik alkol veya disiklopendatien olduğu poliüretanlar kullanılmaktadır. Enjeksiyon ve döngü süreleri parça boyutu ve kullanılan RIM sistemine göre değişmektedir. Tipik bir RIM süreci kalıbı birkaç saniye içerisinde doldurulabilir fakat bazı sistemler gecikmeli reaktivite ile tasarlanmaktadır, böylelikle çok büyük parçalar kalıplanabilmektedir. Çoğu RIM sisteminde kalıplanan parçanın mekanik özelliklerinin iyileştirilmesi ve plastik sisteminin maliyetinin azaltılması için dolgu malzemeleri (cam elyaf, örgü keçeler, sürekli sıralı keçeler veya doğranmış elyaf) bulunmaktadır. RIM ürünleri otomotiv (otomotiv tamponları, çamurluklar ve kaportalar) ve inşaat sektöründe kullanılmaktadır.
Kalıp parçanın şeklini belirlemekte, sıcak plastikleştirilmiş materyali yolluktan kalıp gözüne taşımakta, kapalı kalan hava veya gazı havalandırmakta, parçanın soğutulması ve soğutucu görevi görmekte ve son olarak iz bırakmadan veya hasar vermeden bitmiş parçayı çıkarmaktadır. Kalıplar özel kalıplama çeliği, berilyum bakır, paslanmaz çelik, alüminyum pirinç ve zamak malzemelerinden imal edilmektedir. Bitmiş kalıp yüzeyleri genellikle aşınmanın engellenmesi ve parça enjeksiyonun kolaylaştırılması için parlatılmakta ve kaplanmaktadır. Kalıplar işleme, EDM veya dökme ile üretilmektedir. Kalıp tasarımı, üretimi, işçiliği büyük oranda parça kalitesi ve üretim maliyetini belirlemektedir.
Enjeksiyon kalıbı normalde çeşitli kriterler ile tanımlanmaktadır:
* Kalıptaki gözlerin sayısı
* Yapı malzemesi örneğin; çelik, paslanmaz çelik, sertleştirilmiş çelik, berilyum bakır, krom kaplama alüminyum ve epoksi çelik
* Kalıp çizgisi örneğin; düzenli, düzensiz, iki plakalı kalıp, üç plakalı kalıp
* Üretim yönetimi örneğin; işleme, azdırma, dökme, basınçlı dökme, elektro kaplama ve kıvılcım erozyonu 5.yolluk sistemi örneğin; soğuk, sıcak yolluk ve yalıtımlı yolluk
* Kapılama türü örneğin; kenar, sınırlı (iğne ucu), denizaltı, dökme deliği, halka, diyafram, tab, flaş, fan ve çoklu enjeksiyon yöntemi örneğin; itiş pimleri, sıyırma pimleri, sıyırma tabakası, vida sökme kaması, çıkartılabilir insert, hidrolik çekirdek kolu, pnömatik çekirdek kolu
* İki türde enjeksiyon kalıbı bulunmaktadır, soğuk yolluk ve sıcak yolluklu kalıplar. Yolluk kalıp içerisinde plastiğin plastik enjeksiyon makinesinin ocağından parçaya aktarılmasını sağlayan bir kanaldır. Yolluk kanalı yukarıdaki kalıp türlerinde sıcak veya soğuk durumdadır.
ENJEKSİYON KALIPLARININ TÜRLERİ
İki türde enjeksiyon kalıbı bulunmaktadır. Soğuk yolluk ve sıcak yolluklu kalıplar.
Yolluk kalıp içerisinde plastiğin plastik enjeksiyon makinesinin ocağından parçaya aktarılmasını sağlayan bir kanaldır. Yolluk kanalı yukarıdaki kalıp türlerinde sıcak veya soğuk durumdadır.
SOĞUK YOLLUKLU KALIP
Yolluk çıkartılan ürünün bir parçasıdır ve her baskıda üretilir. Yeniden kullanmak için öğütülür veya hurdaya çıkartılır. Kalıplar basittir ve sıcak yolluklu kalıplardan çok daha ucuzdur. Kalıbın kurulumu ve çalışması için daha az bakım ve daha az beceri gereklidir. Renk değişimi de oldukça kolaydır çünkü kalıptaki tüm plastik her döngüde çıkarılmaktadır. Yaygın Soğuk Yolluklu Kalıp türleri 2 ve 3 plakalı kalıplardır.
İki plakalı kalıpta bir ayrılma düzlemi vardır ve kalıp ikiye ayrılır. Yolluk sistemi bu ayrılma düzleminde yer almalıdır, böylelikle parça yalnızca çevresi üzerinde kapılanabilir. Üç plakalı kalıpta iki ayrılma düzlemi vardır ve kalıp üç bölüme ayrılmakta, kapılama lokasyonunda esneklik sağlamaktadır.
İnsert kalıp – materyalin etrafına plastik kalıplamak için üst kalıptır, metaller veya hatta diğer plastik insertler, sondaj yuvaları için manşonlar, tornavidalar, tutamaklar, elektrik fişleri vb.
2 baskılı kalıplar (aynı zamanda 3 baskılı ve 4 baskılı kalıplar) 2 veya daha fazla renkli parçaların aynı anda üretilmesi için maliyet etkin bir yöntemdir. Logo, trafik veya metin eklemek için ikinci bir süreci ortadan kaldırır.
İstifli kalıplar-iç ve dış dişli parçalar üretmek için kullanılır, örneğin; somun, somunlu matkap, püskürtücü kafaları diğer enjeksiyon kalıp türleri sıyırıcı ejektör kalıp, ayrık boşluklu kalıp ve sürgülü kalıptır.
SICAK YOLLUK
Yolluk kalıp içerisinde yer alır ve sıcaklığın plastiğin erime noktasının üzerinde tutulması için ısıtılır. Böylelikle çok az veya sıfır hurda oluşur dolayısı ile fire ve çapak oluşmaz. Sıcak yolluklu kalıplar yüksek çok gözlü kalıplarda yaygın olarak kullanılır. Sıcak yolluğun en önemli dezavantajı çok daha pahalı olmasıdır, maliyetli bakım ve beceri gerektirir.
SICAK YOLLUKLU KALIPLARIN TÜRLERİ
Harici ısıtmalı tipte, eriyik plastik katı bir manifold ve meme içerisinden akmaktadır. Dahili ısıtmalı tipte, (artık kullanılmamaktadır) plastik doğrudan ince ısıtıcılar üzerinden aşırı büyük yolluklar içerisine akmaktadır. Harici ısıtmalı sıcak yolluk kanallarında herhangi bir yolluk sisteminin en düşük basınç düşüşü bulunmaktadır, renk değişimlerine daha uygundur ve yolluk sisteminde tutarlı eriyik plastik sağlamaktadır. Materyalin takılacağı ve bozulacağı hiçbir nokta yoktur, bu nedenle sıcaklığa duyarlı materyaller için uygundur. Sıcak yolluklarda genellikle kalıbın üretimi ve işletimi daha pahalıdır fakat plastik artığını ve çevrim süresini azaltarak tasarruf sağlamaktadır.
SICAK YOLLUK AVANTAJLARI
* Yollukların çıkartılması ve yeniden öğütme gerekmez
* Kontaminasyon riskini azaltır
* Daha düşük enjeksiyon basınçları
* Daha düşük mengene kuvveti
* Daha kısa soğuma süresi
* Daha düşük baskı gramajı
* Daha temiz kalıplama süreci
* Memenin donmasını engeller
* Kalıp içerisinde tutarlı ısı
DEZAVANTAJLARI
* Sızdırma
* Isıtma elemanı arızası
* Karmaşık ilk kurulum
* Arızalar
* Daha yüksek yatırım maliyetleri
* Daha karmaşık ve pahalı
* Katkılı malzemelerin neden olduğu aşınma
* Hassas materyallerde termal hasar
* Katı sıcaklık kontrolü gerektirir
Ürün Tasarım İpuçları ve Kuralları
Et Kalınlığı: Tüm parçada eşit et kalınlığı kullanın. Bu çekme, büzülme, artık gerilimleri en aza indirgeyecek ve kalıp enjeksiyon ve çevrim sürelerini iyileştirecektir. Kuvvette bozulma olmuyorsa parçayı hızlı soğuma, kısa çevrim süresi ve minimum gramajı sağlamak için minimum duvar kalınlığı ile tasarlayın. Tüm bunlar mümkün olan en düşük parça maliyetini sağlayacaktır.
Kalıplı Menteşeler: Menteşe iki parçayı birleştirirken birinin dönmesini sağlayan bir unsurdur. Buradaki konsept canlı menteşe, integral menteşe veya kalıplı menteşe adını alır ve tek bir operasyonda bunlarla entegre olarak enjeksiyon kalıplanan kapak ve kutu bölümlerini birleştiren ince duvarlı bir bölümden meydana gelmektedir. Tercih edilen materyal esneme yorulmasına karşı en iyi direnç sahibi olan polipropilendir.
* Keskin köşelerden kaçının.
* Menteşenin arka yüzeyini serbest bırakın.
* Polipropilen menteşe için olağan kalınlık 0.25 - 0.50 mm\'dir.
* Akış menteşe içerisinden sağlanmalıdır ve kapı pozisyonu önemlidir.
* Takılma etkileri, kaynak hatları ve aşırı doldurmaya dikkat edin.
* Ayrı bir menteşeli soğutma devresi temin edin.
* Çıkarma sonrasında menteşeyi derhal esnetin.
Köşeler: Gerilim yoğunlukları ve kırılmaları azaltmak için tüm köşeleri iyice yuvarlayın. İç çap en az et kalınlığı kadar olmalıdır.
Koniklik Açısı: Göz veya çekirdekten çıkış yönünde koniklik sağlayarak kalıptan çıkarmayı kolaylaştıracak parçalar tasarlayın. Dokulu yüzeye sahip parçalar, parça kalıptan çıkartılırken dokusu yüzeyde çizik oluşumunu engellemek için daha büyük koniklik açısı gerektirmektedir. Orta seviyede mat veya kumlanmış yüzeyler için 1-3 derece ve kaba yüzeyler için 3-5 derece uygulanmaktadır.
Mesnetler: Mesnetlerin et kalınlığı ana et kalınlığının 9660\'ını geçmemelidir. Taban yarıçapı en az ana et kalınlığının 9625\'i olmalıdır. Bitişik duvarlara bağlanan nervürler veya tabanda köşebentlerle desteklenmelidir. Mesnet köşeye yakın yere yerleştirilecekse nervür kullanılarak yalıtılmalıdır.
Çap: Dış çap X İç çap 2 - 3
Kalınlık: 1/2 - 2/3 nominal et kalınlığı
Köşebent yüksekliği: 2/3 yükseklik
Yükseklik: Tespit elemanı minimum gereksinimler
Koniklik: Her yerde 1 derece
Çap Oranı en az 2 olmalıdır, bu oran arıza riskini azaltacaktır.
Federler (Kayıtlar): Parça sertliğini iyileştirmek için et kalınlığını arttırmak yerine federler veya köşebentler kullanın. Feder uygulaması kalıplı parçanın setliği ve geometrik bütünlüğünü iyileştirmeye yardımcı olacaktır, böylelikle parça ağırlığı, materyal maliyeti ve döngü süresi maliyetlerinden tasarruf edilecektir.
İpuçları: Federlerin kalınlığı bağlandıkları duvarların kalınlığının %50-60 olmalıdır. Federlerin yüksekliği en az et kalınlığının üç katı olmalıdır. Bağlantı noktası yuvarlatılmalıdır. En az 0.250 koniklik açısı uygulayın.
Dip oyulmaları: Harici dip oyulmalarının sayısını en aza indirin. Harici dip oyulmaları yan maçaların kullanılmasını gerektirmektedir, bu durum aletli işleme maliyetini arttırmaktadır. Bazı basit harici dip oyulmaları ayrılma hattının yeniden yerleştirilmesiyle kalıplanabilir.
Kaynak çizgileri: Plastik zıt yönlerde aktığında ve sonunda tekrar bir araya geldiğinde, kaynak çizgileri oluşmaktadır. Kaynak çizgileri kalıplama sırasında plastiğin akış yüzeylerinin birleştiği yerde oluşmaktadır. Kaynak çizgi bölgesi kırılmalar ve gerilim çatlamasına karşı daha eğimlidir.